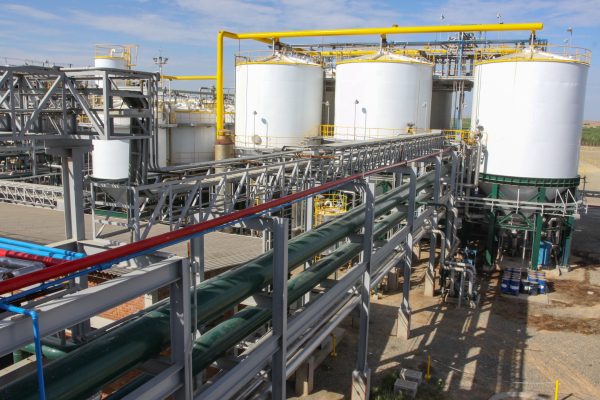
Cuando hablamos de combustibles renovables con el público en general, muchos podrían imaginar autos que funcionan con gasolina hecha de flores silvestres y hierba de pradera. Aquellos que trabajan en la industria reconocen que las grasas y aceites utilizados para fabricar diésel renovable pueden ser cualquier cosa menos eso, y de hecho, muchos provienen de fuentes poco románticas, como desechos de mataderos.
Desde el punto de vista del proceso, las fuentes de desechos pueden causar problemas serios porque esas grasas y aceites pueden contener contaminantes corrosivos, mucho peores que cualquier cosa que se encuentre rutinariamente en las operaciones de refinación convencional. El consejo sobre cómo los productores de diésel renovable y combustible de aviación sostenible (SAF) pueden lidiar con estos problemas es el tema del artículo en dos partes en Hydrocarbon Processing, Implementar Soluciones Innovadoras de Gestión de Corrosión para la Refinación de Biocombustibles.
La Parte 1 está en la edición de septiembre. Los productores deben entender que encontrarán estos contaminantes, y que estos afectarán los equipos, pero el efecto puede ser gestionado.
Las materias primas limpias de semillas oleaginosas son fáciles de trabajar pero se extraen de los suministros de alimentos. Los productores que desean encontrar las alternativas de menor costo y evitar contribuir a la inseguridad alimentaria global seguramente se enfrentarán con grasas animales y desechos de cultivos difíciles.
Como con todos los productos de desecho, hay desafíos de calidad constante de la materia prima y cadenas de suministro confiables. Las impurezas de empaque de polietileno se encuentran típicamente en las grasas animales, resultando en desafíos de proceso con desactivación de catalizadores, preocupaciones de ensuciamiento con intercambiadores de calor, y restricciones de flujo y caídas de presión en lechos de catalizadores provocadas por obstrucciones. En general, estos tipos de aceites de desecho requieren tuberías de alimentación con rastreo de calor debido a su menor punto de nubosidad.
Obviamente, estos son problemas, pero la corrosividad puede ser un problema aún más serio.
Aunque los componentes orgánicos de azufre en los renovables disminuyen en comparación con las materias primas de petróleo, el aumento de la afluencia de cloruros y nitratos orgánicos crea desafíos con la integridad de los equipos de proceso y las tuberías aguas abajo de las unidades de hidrotratamiento. Además de estas y otras sustancias que aceleran la corrosión, la presencia de agua facilita los mecanismos de corrosión al proporcionar un camino electrolítico. El agua solubiliza ácidos orgánicos e inorgánicos, creando dióxido de carbono a través de la hidrodescarboxilación, lo que convierte los cloruros orgánicos en ácido clorhídrico y promueve la corrosión influenciada microbiológicamente.
El artículo entra en más detalle sobre dónde tienden a ocurrir estos procesos y qué tipos de corrosión son los más comunes. Los problemas de corrosión a menudo provienen de las refinerías que reutilizan equipos de proceso antiguos para este nuevo uso. La metalurgia utilizada en ese equipo probablemente fue diseñada para manejar materias primas de petróleo crudo convencionales, que típicamente son mucho menos corrosivas. El resultado inevitable será que este equipo sufra pérdida de metal. Los operadores deben monitorear la pérdida para evitar una falla catastrófica inesperada de un accesorio de tubería o la pared de un recipiente. La respuesta es el monitoreo continuo del grosor del metal en puntos estratégicos utilizando sensores ultrasónicos, como los Sensores de Monitoreo de Corrosión y Erosión Inalámbricos Rosemount™ Wireless Permasense WT210 de Emerson.
Los sensores de monitoreo ultrasónico inalámbrico de grosor de pared instalados permanentemente abordan estos y otros problemas, siendo la mejor opción para la mayoría de las aplicaciones de monitoreo de corrosión a alta temperatura. Estos sensores pueden medir pequeños cambios en el grosor de la pared y exhibir robustez ante condiciones extremas de la planta, además de tener una vida útil de batería extendida para proporcionar una operación confiable durante todo el ciclo entre paradas.
En la Parte 2, veremos estrategias para crear un programa integral de monitoreo de corrosión. Para obtener más información, visite las páginas de Monitoreo de Corrosión y Erosión de Emerson en Emerson.com. También puede conectarse e interactuar con otros ingenieros en los Grupos de Petróleo y Gas en la comunidad Emerson Exchange 365.